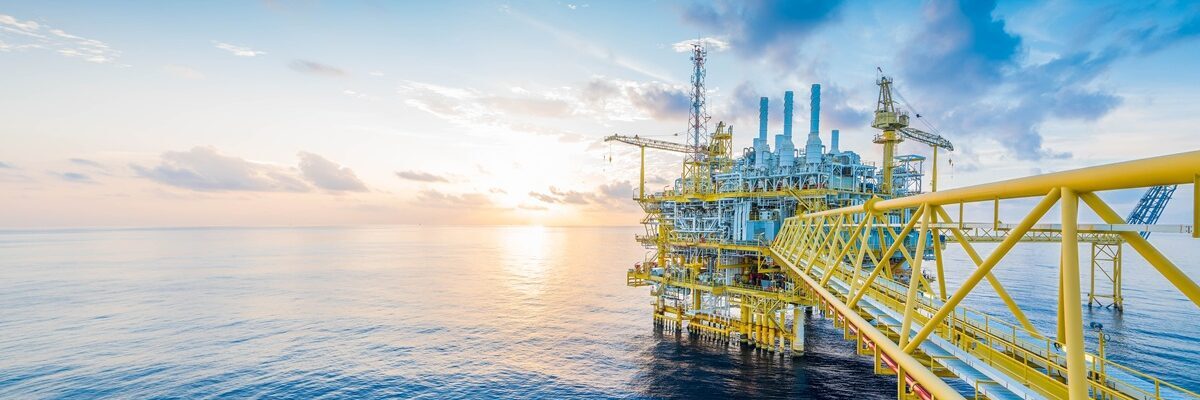
Advanced Engineering Solutions for Offshore Water Injection
Project Overview
Trillium Flow Technologies delivered specialized water injection pumps for a major offshore installation in the Middle East region. This project highlights our engineering excellence in designing and manufacturing high-performance pumping solutions for the most demanding offshore applications.
Customer Challenge
The project required the supply of four high-pressure water injection pump systems for an offshore platform. These pumps would be critical for maintaining optimal field production by injecting seawater into the reservoir formation.
The technical challenges were significant:
- Designing pumps capable of handling extremely high pressure (2,160 m head) while handling corrosive seawater.
- Balancing mechanical requirements with metallurgical limitations of specialized materials.
- Engineering a solution for installation on an offshore platform, meeting constraints related to limited space and deck movement/deformation.
The Trillium Solution
Our approach incorporated a comprehensive engineering process:
Pump Specifications
- Trillium provided four API 610 BB5 multistage pumps with the following specifications:
- Flow rate: 300 m³/h
- Head: 2,160 m
- Drive: 3 MW electric motor at 3,000 RPM
- Materials: Super duplex stainless steel for wetted components
- Configuration: Back-to-back impeller arrangement
Innovative Design Features
Back-to-Back Impeller Configuration
Our engineering team implemented a back-to-back impeller solution that provides two critical advantages:
- Balanced hydraulic thrusts for improved reliability
- Reduced thickness of barrel casing components
Advanced Materials Engineering
- The pumps feature optimized super duplex stainless steel components, selected to provide:
- Superior corrosion resistance against seawater
- Excellent mechanical properties under high pressure
- Optimized casting thickness to balance strength and manufacturability
Specialized Mounting System
- Baseplate installed on 3-point gimball mountings to reduce stress transfer between the platform and pump system
Comprehensive Auxiliary Systems Integration
- Double mechanical seal with API 11/62 plan system
- API 614 lubrication system
- API 671 coupling
- External API 661 air-oil heat exchanger
Advanced Engineering Methods
Our development process employed several cutting-edge engineering techniques:
Computational Fluid Dynamics (CFD)
Extensive CFD analysis was conducted on the crossover related to the back-to-back impeller configuration to detect possible complications such as:
- Anomalous flows
- Performance and pressure losses between stages
- Pre-rotation phenomena
The analysis led to the optimization of the crossover design, which included:
- The improvement of channels’ section
- The addition of flow rectifier in specific directions
- The upgrade of the shape of deflectors
- The optimization of blades and of the inclination angles of borders
Finite Element Analysis (FEM)
FEM modeling was crucial for:
- Verifying stress levels in pressure-containing components such as the sheer rings
- Optimizing the design of the baseplate to accommodate platform movement
Material Science
Close collaboration between our engineers, foundry specialists, pattern makers, and the EPC’s material engineering experts allowed us too mitigate strength and manufacturability and mechanical features of the pressure components in super duplex. For instance, optimal casting processes were developed for the barrel casing to achieve consistent mechanical properties and prevent severe defects such as the formation of fragile phases in the material.
Manufacturing Excellence
All pumps were manufactured at Trillium’s specialized workshop facilities, where strict material handling procedures and specialized machining techniques were adopted to address the challenges of super duplex stainless steel.
Comprehensive Testing
Each complete pump unit underwent string testing at our advanced test center. The test included the pump units’ noise hoods to guarantee the requested noise level.
Conclusion
This project demonstrates Trillium Flow Technologies’ position as a leader in the high-value offshore pump market. By combining innovative engineering, advanced computational analysis, materials expertise, and rigorous quality control, we delivered a solution perfectly matched to the demanding requirements of offshore water injection service.
Our investment in engineering, R&D, manufacturing, and testing capabilities specifically geared toward complex offshore applications continues to strengthen our position in this challenging market segment.
Contact Us
For more information about our capabilities in FLNG and offshore applications, please contact your Trillium representative or click here to contact us to have your inquiry immediately routed to our sales team.