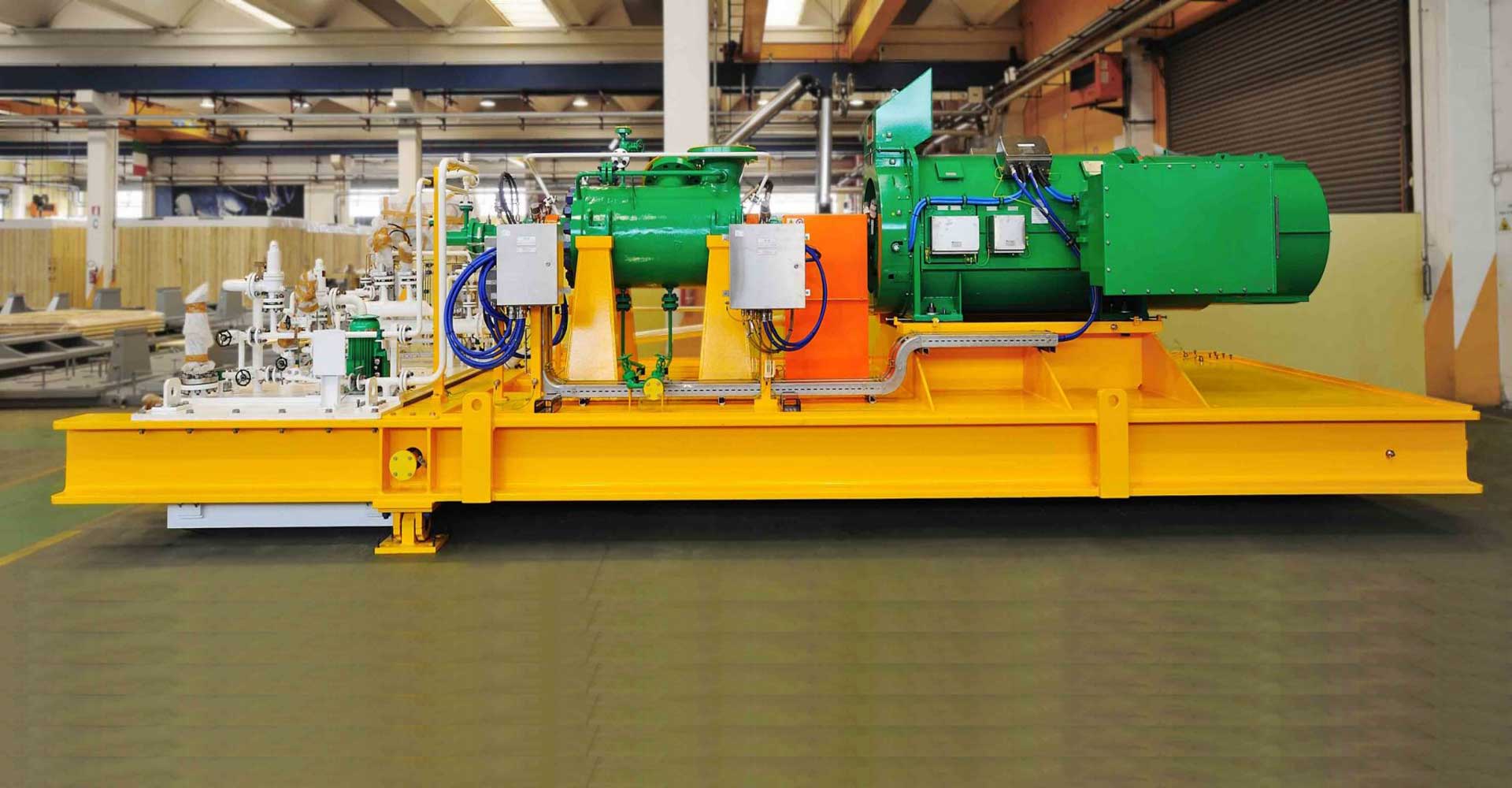
Over the past few years, an increase in demand and production of Oil and Gas has pushed the industry towards new technologies and more efficient processes to off-shore reserves. Floating Production Storage and Off-loading (FPSO) and Floating Liquefied Natural Gas (FLNG) units have played a major role in meeting this demand with the capability to extract and refine oil and gas directly on-site.
These floating units require state-of-the-art design to deliver on tight time schedules while providing maximum reliability in extreme conditions. This is achieved through utilizing modules, skidded equipment, and packages that are ready to be assembled on the FPSO and commissioned as soon as possible.
Pumping equipment, widely used in several on-board processes, is designed and provided as ready skids; although this is a common practice for on-shore projects, there are several special features required to match the demanding environment and safety restrictions of FPSO and FLNG.
Because installations are on large ship hulls, movement of the ship and deck flexibility has to be considered during baseplate design, from both a static and dynamic (vibration) point of view. From a static perspective, there are increased loads on the baseplate due to accelerations in all directions of the ship – from towing and transportation, normal production activity, and severe conditions such as violent storms and hurricanes. Furthermore, the pumps must operate without any of the problems that can be caused by the inclination to the horizontal plane, caused by waves against the FPSO or FLNG. Another important requirement to ensure highly reliable equipment is vibration control of the entire skid, which has to be connected directly to the frame structures of the FPSO or FLNG modules. Deck stiffness and the natural frequency of the skid must be considered to ensure appropriate separation margin with main exciting forces (1xrpm , 2xrpm , n° Vane X rpm) of the pump.
Anti-Vibration Flexible Mountings (AVM) and three points Gimbal mountings are used to "isolate" the biggest skid from deck deformations. These components are a very important part of the biggest skid, to avoid misalignment of driven equipment and its driver from deck movements and induced floating and production loads on the structure.
With anti-vibration flexible mountings, flexible pads are installed between the skid and the main frames, allowing the frame to "deform" with inducing high loads to the skids itself. The number of pads is selected considering required stiffness (for natural frequency calculation) and skid mass (limiting total deflections). Flexibility can be provided by springs or through polymeric (rubber type) pads layered between steel plates where equipment and skids are connected. These pads are extremely useful to dynamically isolate the equipment and with polymeric pads to increase the vibration-damping capability.
Three-point gimbal mountings instead rely on "three spherical hinges" that can absorb all the equipment weight but at the same time accommodate the deformation and rotations of the deck. The "gimbal" is a robust hinge that includes maintenance free "sealed for life" spherical bearings; proper orientation of each gimbal allows for the accommodation of all deck movement and rotations, providing higher stiffness to support the heaviest skids.