What Are the Different Types of Butterfly Valves?
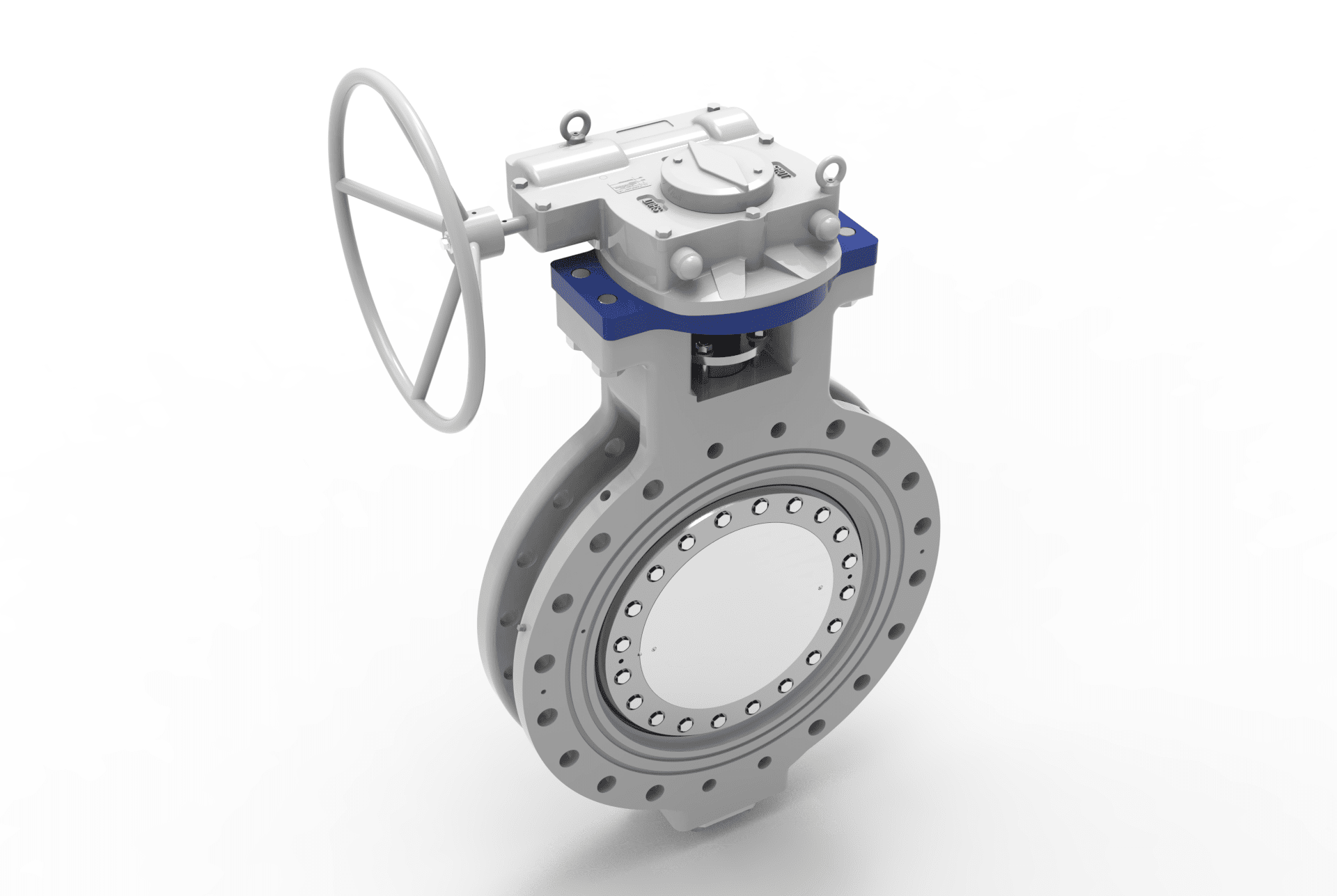
Butterfly valves are a type of quarter-turn isolation valve that offers quicker opening and closing than valves with linear travel. They’re commonly used in a wide range of industrial applications, including midstream and downstream oil and gas production, nuclear power generation, and chemical processing.
There are many types of butterfly valves, with the differences between them based on design features, connections, seat materials, and actuation methods. Each type of butterfly valve has characteristics that make it a better fit for certain applications, pressures, and flow rates. Understanding the differences between each type of butterfly valve is critical to finding the right valve for your application.
Butterfly Valves by Design Type
Concentric Butterfly Valves
Concentric butterfly valves are designed to solve the tightening problems that can occur between the disc and seat of the butterfly valve. The stem and disc of the valve are situated in the center, and it creates a seal when the disc deforms the soft seat, causing full friction during the whole operating cycle. This valve can handle chemicals, coatings, food, some solids, and abrasive applications. One advantage is that most of the media flowing through the valve will not contact the body since the valve seat covers the body.
Double Offset Butterfly Valves
Double offset, or double eccentric, butterfly valves operate with the stem center deviated from the center of the disc and valve. With this structure, the valve disc can leave the valve seat quickly, greatly reducing unnecessary over-compression and scraping between them. This design also helps decrease the wearing process while extending the operational life of the valve. The reduction in scraping allows the seats of these valves to be made from metal, expanding the application range of butterfly valves to high-temperature applications.
One example of a double offset butterfly valve is the Batley Valve® Metalseal Butterfly Valve. This valve’s double offset design and metal seal work together to ensure a uniform 360º seal contact in the closed position, making it a suitable option for higher pressure and temperature applications.
Triple Offset Butterfly Valves
Also known as triple eccentric, a triple offset butterfly valve is designed to eliminate the rubbing between the seat and seal ring through the flow path, reducing seat and seal wear and extending cycle life. They are used in applications similar to gate valves, where a metal seat is required and tight shutoff and/or quarter-turn actuation is desired. However, triple offset butterfly valves can open and close more quickly and can be frequently operated, even if there is an emergency shutoff. This valve has low torque and is recommended for both high and low-temperature applications.
The TRICENTRIC® Triple Offset Butterfly Valve, for example, features a triple offset metal seat design that allows for a very tight metal seal at temperatures in excess of 1,500º Fahrenheit. With its bidirectional, tight sealing, and excellent throttling characteristics, this valve is well-suited for isolation, high temperature, cryogenics, nuclear containment, and other harsh service applications.
Butterfly Valves by Design Type
Metal-Seated Butterfly Valves
A metal-seated butterfly valve’s seat and disc sealing surfaces are made of metal, allowing the valve to handle corrosive materials and high-temperature, high-pressure applications. The triple-offset butterfly valve from Tricentric®, for example, features a metal seat that helps provide excellent flow and control characteristics, sealing capabilities, and dependability in a wide range of industrial applications.
Soft-Seated Butterfly Valves
As the name suggests, a soft-seated butterfly valve has seat materials made with non-metallic materials like rubber or PTFE. Soft-seated butterfly valves offer reliable sealing for lower temperatures and pressures. The difference between soft-seated and metal-seated butterfly valves is that soft seats provide zero leakage while metal seats offer acceptable leakages depending on the application. Because the seat material is soft, it is also easier to replace than the seat on metal-seated butterfly valves. Soft-seated butterfly valves excel in water treatment and food and chemical processing applications.
Butterfly Valves by Connection Type
All the above butterfly valve types can be configured with the following connection types:
Wafer-Style Butterfly Valves
Wafer-style butterfly valves provide the lowest installation cost of any butterfly valve. Wafer valves are placed between two flanges to allow flow and sealing against bidirectional differential pressures and backflow in universal flow systems. They are available in zero-offset, double-offset, and triple-offset designs.
Lug-Style Butterfly Valves
Wafer-style butterfly valves provide the lowest installation cost of any butterfly valve. Wafer valves are placed between two flanges to allow flow and sealing against bidirectional differential pressures and backflow in universal flow systems. They are available in zero-offset, double-offset, and triple-offset designs.
Flanged-Style Butterfly Valves
Flanged-style butterfly valves use a centrally mounted vain or disc on a stem, shaft, or flange. This acts as the axis for the rotating disc. With two valves on either end, flanged-style valves have a bigger face-to-face than wafer or lugged valves.
Butterfly Valves by Actuation Method
Manual Actuation
A manual actuator butterfly valve, also known as a manually operated butterfly valve, is a type of butterfly valve equipped with an actuator operated by a crank, lever, or wheel. Generally inexpensive, manual actuators are typically used on smaller butterfly valves that don’t need to open and close quickly.
Electric Actuation
Instead of operating by hand, electric actuators open and close via a remotely controlled motor that can open and shut the butterfly valve quickly. Often low-maintenance, electric actuated butterfly valves are best suited for non-critical process applications.
Pneumatic Actuation
A pneumatic actuated butterfly valve uses the force of compressed air to open and close the disc within the valve, thus controlling the flow of fluids and gasses within a pipeline. Pneumatic actuators are typically lightweight, compact, easy to maintain, and offer swift opening and closing without the need for manual operation. They are available in two configurations: single-acting or double-acting.
Single-acting actuators use a spring to automatically close or open the valve in case of some kind of failure, while double-acting actuators open and close with the force provided by moving air. Pneumatic actuated butterfly valves are commonly used in the chemical processing, water treatment, and oil and gas sectors.
Hydraulic Actuation
A hydraulic actuator on a butterfly valve uses hydraulic pressure to open and close the valve. These actuators are most often equipped on larger valves that require a significant amount of force to operate. In addition to having a great degree of torque, hydraulic actuators can operate without an extra power source during a power outage. These actuators are commonly deployed on butterfly valves used in high-pressure or heavy-duty applications.
Butterfly Valve Size Ranges
Butterfly valves can come in a variety of sizes depending on the brand and model. For example, the BV 22000 Hyperseal ranges from two to 64 inches while the BV 26000 Metalseal goes from six to 80 inches. There are numerous options within these ranges including the popular 16-inch butterfly valve option.
Trillium Flow Technologies™ Butterfly Valve Brands
Butterfly valves come in a variety of designs and materials that are all specific to the systems involved. Choosing the right valve is essential for the success of any flow control system. The Trillium Flow Technologies™ brands, TRICENTRIC® and Batley Valve®, deliver outstanding value in their range of butterfly valves. They are highly engineered, meet stringent industry requirements, and provide low cost of ownership to the end user through improved life cycle costs, emissions control, reduced downtime, and lowered maintenance costs.
You can count on Trillium Flow Technologies™ valves for complete flow control success. Our reliable legacy brands, like TRICENTRIC® and Batley Valve®, and team of dedicated support and services experts, ensure that you have a trusted partner who adds value at every phase of your project cycle. You’ll have confidence in your flow control now and in the future.